تحلیل حالات و آثار خرابی (FMEA)
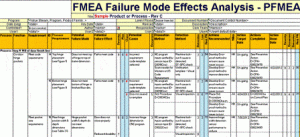
تحلیل حالات و آثار خرابی (FMEA)
مثال های متنوعی در مورد مرجوعی به دلیل طراحی نامناسب محصولات وجود دارد. خرابی محصولات می تواند ناشی از مجموعه ای از اشتباهات در هنگام طراحی ، تولید ، تامین مواد ، کنترل کیفی ، توزیع و سایر فرآیندهای چرخه تولید باشد. تحلیل حالات و آثار خرابی (FMEA) روشی است برای تعیین و شناسایی اشتباهات و عیوب ممکن در هنگام فرآیند طراحی و ساخت. در کل دو دسته اف ام ای اِی وجود دارد: DFMEA و PFMEA. در DFMEA که سعی در شناسایی عیوب فنی تولید ، کاهش عمر محصول ، ایمنی و استانداردهای حاصل از
- مشخصات مواد
- هندسه
- تلرانس
- ارتباط و اتصال به سایر قطعات و سیستم ها
- نویز مهندسی دارد.
در PFMEA سعی در شناسایی عیوب و نواقصی است که بر کیفیت محصول ، کاهش قابلیت اطمینان فرآیند ، عدم رضایت مشتری ، ایمنی یا خطرات محیطی نظیر موارد زیر تاثیر می گذارد.
- عوامل انسانی
- روش های مربوط به هنگام فرآیند
- مواد مورد استفاده
- ماشین ها و دستگاه های استفاده شده
- سیستم های اندازه گیری تاثیرگذار بر پذیرش
- فاکتورهای محیطی بر عملکرد فرآیند
چرا لازم است تحلیل حالت ها و اثار خرابی (FMEA) انجام شود؟
به طور کل هرچه علت خرابی زودتر تشخیص داده شود، هزینه کمتری برای تولید کننده خواهد داشت. هرچه خرابی دیرتر تشخیص داده شود، هزینه های آن به صورت نمایی بیشتر خواهد شد.
چه زمانی تحلیل حالت ها و اثار خرابی انجام شود؟
- هنگامی که یک محصول ، فرآیند یا خدمت جدید طراحی می شود
- هنگامی که برنامه برای تغییر فرآیند موجود با یک روش جدید وجود دارد
- هنگامی که هدف، بهبود کیفیت یک فرآیند مشخص باشد
- هنگامی که نیاز به شناسایی و بهبود نقوص فرآیند وجود دارد
علاوه بر این موارد، امکان اجرای اف ام ای اِی در هنگام سرویس دهی محصول وجود دارد. برای اطلاعات بیشتر در مورد آنالیز خرابی در قطعات ، تجهیزات و سازه های مهندسی اینجا کلیک کنید.
خدمات و منتورینگ بنوموسی
شرکت بنوموسی با ارائه جلسات منتورینگ آباکوس راهنمای شما عزیزان در جهت رفع و بهبود ایرادات فنی و مهندسی پروژه های صنعتی و دانشجوی تان در زمینه مدلسازی، تحلیل، و صحتسنجی نتایج می باشد. این جلسات به صورت آنلاین و حضوری برگزار میشود و نیم ساعت اول رایگان است. برای اطلاعات بیشتر و رزرو وقت، از صفحه منتورینگ اباکوس ما دیدن کنید.
برای استفاده از خدمات شبیهسازی و مشاوره رایگان ما، کافی است با ما تماس بگیرید. ما در تمام مراحل پروژه کنار شما هستیم تا بهترین نتایج را بهدست آورید.
برای کسب اطلاعات بیشتر و دریافت منتورینگ ، لطفاً با ما تماس بگیرید یا از وبسایت Banumusagr بازدید کنید. تیم ما آماده است تا شما را در دستیابی به نتایج مطلوب در تحلیلهای عددی و شبیهسازیهای مهندسی یاری کند.
راه های ارتباطی با شرکت بنوموسی :
TELEGRAM : https://t.me/BanuMusaGr
ایمیل: info@BanuMusaGr.com
تلفن همراه: 388 20 55 0915
تلفن: 35424520– 51 (98+)
آدرس: مشهد – کیلومتر 12 بزرگراه آسیایی (جاده قوچان)- جاده شهرک صنعتی توس- شهرک فناوری صنایع غذایی و بیوتکنولوژی شمال شرق- معاونت صنایع کوچک- مرکز خدمات.
تحلیل حالت ها و اثار خرابی FMEA چیست؟
FMEA یک روش سیستماتیک است که به شناسایی و تجزیه و تحلیل اشتباهات، عیوب و خرابیهای ممکن در فرآیند طراحی و تولید کمک میکند. این تحلیل به منظور کاهش خطرات و بهبود کیفیت محصول یا فرآیند انجام میشود.
چه نوع FMEAهایی وجود دارد؟
دو نوع اصلی FMEA وجود دارد:
DFMEA (Design FMEA): برای شناسایی مشکلات فنی در طراحی محصول، مانند خرابی ناشی از مشخصات مواد، تلرانسها، اتصالات و غیره.
PFMEA (Process FMEA): برای شناسایی عیوب و نواقص در فرآیند تولید که ممکن است بر کیفیت محصول، قابلیت اطمینان فرآیند و رضایت مشتری تأثیر بگذارد.
DFMEA در چه مواردی به کار میرود؟
DFMEA به منظور شناسایی عیوب مرتبط با:
مشخصات مواد
هندسه و تلرانس
ارتباط و اتصال به سایر قطعات
نویز مهندسی انجام میشود.
PFMEA چه عواملی را در نظر میگیرد؟
PFMEA به شناسایی و کاهش عیوبی که بر کیفیت محصول یا فرآیند تأثیر میگذارند، میپردازد. این عیوب میتوانند به عواملی مانند:
عوامل انسانی
مواد مورد استفاده
ماشینآلات و دستگاههای تولیدی
سیستمهای اندازهگیری
فاکتورهای محیطی مربوط باشند.
چرا اجرای FMEA ضروری است؟
شناسایی زودهنگام مشکلات و خرابیها میتواند هزینههای ناشی از تعمیر یا تغییرات را کاهش دهد. هرچه خرابی دیرتر شناسایی شود، هزینههای تولید و اصلاح به صورت تصاعدی افزایش خواهد یافت.
چه زمانی باید FMEA انجام شود؟
هنگام طراحی یک محصول، فرآیند یا خدمت جدید
هنگام تغییر فرآیندهای موجود با روشهای جدید
هنگام نیاز به بهبود کیفیت فرآیند یا محصول
هنگام شناسایی و بهبود نقایص موجود در فرآیند
آیا میتوان FMEA را در طول سرویسدهی محصول انجام داد؟
بله، FMEA را میتوان در طول مراحل سرویسدهی و نگهداری محصولات نیز اجرا کرد تا مشکلات و خرابیهای ممکن در زمان بهرهبرداری شناسایی و رفع شوند.
چگونه میتوان اطلاعات بیشتری درباره آنالیز خرابی دریافت کرد؟
برای اطلاعات بیشتر درباره تحلیل خرابی در قطعات، تجهیزات و سازههای مهندسی، میتوانید از لینک مربوطه استفاده کنید.